
I was mulling over filler piece ideas for my TEOTWAWKI project. One of the ideas I came up with was dragon's teeth, you know those big concrete anti-vehicle things. Nothing says war zone more than they do, right? So I set out and made a piece with three of them on it. As I was sitting there looking at it, contemplating how to paint it, I was struck with the idea that it made a perfect piece for me to try and cast, so I broke out the kit.
(This next part is going to be old hat for those who have done casting, before. My hopes are that any novices will see how easy it is and give it a try. Plus I like hearing myself talk...or type as the case may be.)
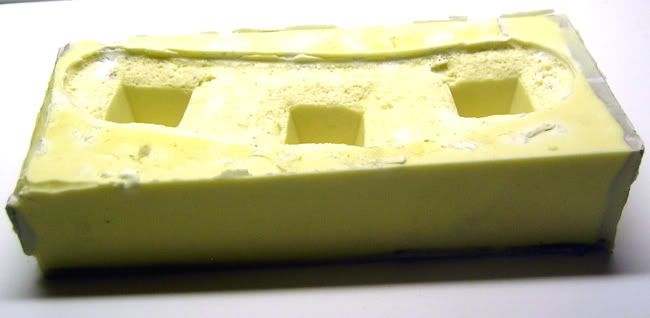
I was able to remove the box after about 4 hours. I let the mold cure over night. The discoloration in the pic are due to two things. The grey is the clay I used to seal the inside of the box and the white is due to not mixing the RTVR thoroughly. Neither one of which caused an issue. Next time I make a mold, I am going to use something like pink foam to act as a filler, so I don't use as much RTVR.
The following morning I set about making some casts. Following the directions I mixed the 2 part resin. I ended up wasting about 1/2 of what came in the kit, trying to figure out how much to use in the mold. I mixed WAY too much on the first couple of attempts. It took a lot less than I anticipated. One thing about the resin, once you start mixing, there is no going back. It starts setting in about a minute. It is a big time saver, as I was able to turn out a workable cast in about 15 minutes; that from mixing to final sanding. In the end, I was able to get 7 casts in less than 2 hours time. That is a lot less than it would have taken making them by hand. Plus, they are a lot more durable than the original master. The picture to the left shows the casts, along with the painted up master.
Below, you can see more detail on the finished master, with a couple of 25mm minis for scale. I am going to put a couple of the casts under the knife and add some battle damage to them. These will definitely work on my PA table. If I did 28mm WWII, they'd work perfectly there, too.
In the end, I learned a lot and had an enjoyable time to boot. I think I may remaster this piece; changing dimensions ans adding a bit of detail. Also, I have to work out the fiscal aspect of casting more, and different items. The RTVR and resin can be a bit pricey. If the costs work out right, hopefully I can finance casting stuff for my own table by selling stuff to others for theirs, if not put a little extra change in my pocket.
They look fantastic -and many thanks for the tutorial too.
ReplyDelete